Green news: Automotive pilot project launched to address ELV plastic waste; SK Chemicals to set up recycling centre in South Korea
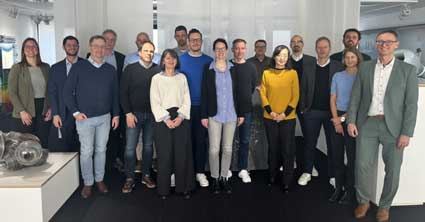
The Global Impact Coalition (GIC), a CEO-led collaborative platform originally incubated at the World Economic Forum, has launched what it says is the world’s first Automotive Plastics Circularity pilot together with seven companies from the chemical and recycling industries: BASF, Covestro, LyondellBasell, Mitsubishi Chemical Group, Sabic, Suez, and Syensqo. This pilot platform will address the critical challenge of recycling plastics from End-of-Life Vehicles (ELVs).
Every year, over 800 million tonnes of ELV plastics are incinerated or landfilled in the European Union alone, resulting in significant economic losses and environmental impact. The GIC pilot project aims to address this issue, enabling the automotive industry to significantly increase the rate of closed-loop recycled plastics, by transforming ELV plastic waste into valuable resources.
Taking place at sites in the Netherlands and Germany, the pilot project will be used to test and optimise a new approach to dismantling, sorting and recycling plastic fractions, helping to build a business case for broader industry adoption, starting in the EU.
It adds that 100 ELVs will be dismantled into plastic parts, which will be shredded and sorted into ten different polymer groups. These will then be recycled by Syensqo and the other chemical companies taking part in the project.
To ensure the pilot’s success, the seven project partners have engaged dismantlers, shredding companies and sorting facilities. By pooling demand for a wide variety of ELV polymers, the initiative aims to demonstrate the economic feasibility of large-scale closed-loop recycling systems and help overcome longstanding challenges, such as high manual processing costs, inefficient sorting methods and limited recovery expertise.
The Automotive Plastics Circularity project aligns with evolving regulatory frameworks, including the EU’s proposed ELV regulations, which currently mandate that by 2030, 25% of plastics in new cars must come from recycled materials, with 25% of those derived from closed-loop recycling (from end-of-life vehicles). This pilot aims to validate the scalability of solutions capable of achieving these targets, ensuring significant impact and reducing the current reliance on landfilling and incineration.
GIC says it invites stakeholders across the automotive and recycling value chains to join this effort.
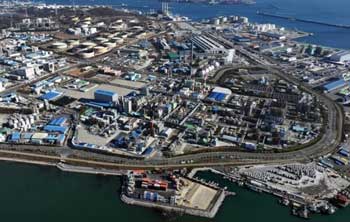
Meanwhile, in other news, South Korea’s SK Chemicals, which claims it is the first company in the world to successfully mass-produce chemically recycled materials, has embarked on establishing a comprehensive plastic recycling solution centre in the country. This centre will encompass the production of circular recyclable raw materials, demonstration research, and material production.
The company says that the Recycle Innovation Centre (RIC) will be set up at its Ulsan plant where eco-friendly chemical materials are produced. The company will invest in new pilot facilities for the chemical decomposition of waste plastics to produce recycled BHET (r-BHET), linking them with existing commercial copolyester production facilities.
The depolymerisation pilot facility is scheduled to begin operations in 2026 with an annual production capacity of 50 tonnes. BHET(r-BHET), an intermediate raw material for polyester-based materials such as PET and copolyester, is integral to SK chemicals' chemical recycling technology.
This marks SK chemicals' first depolymerisation technology-based recycling centre in South Korea.
The newly constructed depolymerisation pilot facility will produce recyclable plastic raw materials (r-BHET) from waste plastics. This facility will validate commercialization technology for various types of low-quality waste plastics that were previously difficult to recycle using conventional methods, expanding beyond typical transparent bottles to include fibres, films, and automotive parts.
In particular, the recycling of textiles is known to be highly challenging field due to the diverse forms and types of materials mixed in a single garment. This includes not only polyester yarn but also other fibres such as cotton, as well as various accessories like buttons.
With the construction of the RIC, SK chemicals will establish an integrated research and production system at its Ulsan plant, covering everything from circular recycled raw materials (r-BHET) to circular recycled materials. All processes from depolymerisation to demonstration research, polymerisation, and mass production will be organically integrated at one location. This is supported by a polymerisation pilot that produces a circular recycled PET and a commercial production facility capable of mass-producing circular recycled copolyester.
Completion of RIC is expected to accelerate implementation of SK Chemicals' Closed Loop solution, which is a complete circular system where waste plastics previously destined for landfills or incineration are subjected to collection, crushing, cleaning, depolymerisation, and polymerisation to be reproduced in a form identical to petroleum-based plastics and then used to manufacture products such as electronics and beverage containers.
While recycled plastics from collected waste PET bottles are primarily repurposed into fibres for initial recycling, most fibre products currently end up being incinerated or landfilled after use.
Depolymerisation-based circular recycled materials are recognised as a technology capable of achieving a complete circular structure as it breaks down waste plastics at the molecular level to achieve properties and quality identical to petroleum-based materials. This enables water bottles to be recycled back into water bottles and waste electronic plastics back into electronic products.
The company adds it is strategically developing industry-optimised depolymerisation technology and expertise to establish a foundation for large-scale production facilities.
SK Chemicals says it has a strong track record in recycling: It was the first globally to commercialise recycled copolyester using chemically recycled raw materials (2021); the first in South Korea to supply recycled PET (2022); and has established a solid production base for recycled waste plastic business by acquiring a stake in Chinese company Shuye Environmental Technology and establishing SK Chemicals Shantou.
Subscribe to Get the Latest Updates from IMA Please click here
©2025 Injection Moulding Asia. All rights reserved.