Der Grüne Punkt/Haitian/ExxonMobil collaborate in toy project incorporating rPP
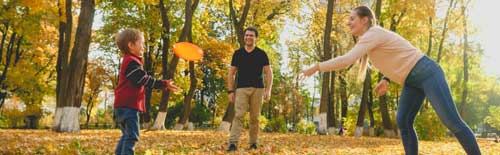
In pursuit of plastic circularity goals, manufacturers of plastic goods are looking for more ways to support the collection of plastic waste and potential diversion from landfills and incineration.
Mechanical recycling breaks down plastic materials into pellets or shreds, which are then melted or mixed with other components to create new plastic products. The practice helps contribute to a more circular plastics economy, which seeks to create value from used materials, instead of disposing of them once they have reached their conventional end of life. While mechanical recycling is expected to continue to play a role in the circular plastics economy, but it has limits. Because polymer performance often declines through the mechanical recycling process, the resulting products with recycled content can have lower performance than plastics made from virgin feedstock. The challenge is to get products with mechanically recycled content that meet higher performance standards.
Recycling solutions provider Der Grüne Punkt needed a way to help brand owners meet their sustainability goal of incorporating more recycled content into their products. However, achieving the right combination of mechanical strength and flexibility from products with recycled plastic content remained a challenge.
Der Grüne Punkt teamed up with ExxonMobil Signature Polymers and Chinese machine maker Haitian to tackle this challenge in the production of flying disc toys using a 5-10% dose of ExxonMobil’s Vistamaxx performance polymers on Haitian’s fifth generation injection moulding machines.
Vistamaxx performance polymers compatibilised well with the PP recyclate from Der Grüne Punkt.
Thus, ExxonMobil says its technology and Der Grüne Punkt worked together to optimise the right Vistamaxx ratio to use to balance and optimise properties of the flying disc toys.
Meanwhile, Haitian optimised settings on its machinery achieving 20-40% energy savings compared to the previous machine generation.
Blending 10% Vistamaxx with Systalen PP-C15001 recyclate from Der Grüne Punkt allowed significant improvement in both the mechanical properties of the flying disc toys and the processability.
The companies say the results were impressive:
- Improved strength: The impact strength of the product with recycled content at room temperature improved by 38%, while at 0°C, it was boosted by 39%, making the discs tougher and more durable.
- Better flexibility: Flexural modulus decreased by 25%, giving the final product the perfect balance between strength and flexibility.
- Faster, more efficient production: The melt flow rate (MFR) increased by 14%, potentially allowing for faster production times and reduced energy consumption.
The above success showcases how collaboration across the value chain can help businesses meet their sustainability goal of incorporating recycled content in their products.
Subscribe to Get the Latest Updates from IMA Please click here
©2025 Injection Moulding Asia. All rights reserved.