Battery recycling: Li-Cycle in recycling partnership for German facility; Altilium recycling LFP EV batteries for global OEM
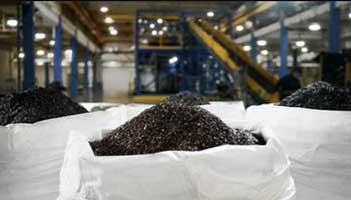
Lithium-ion battery resource recovery company Li-Cycle Holdings Corp. says it has partnered with an additional premium automotive original equipment manufacturer (OEM) to recycle lithium-ion battery materials at its Germany Spoke facility as it continues to broaden its commercial footprint in the EU.
This exclusive agreement channels feedstock from a facility producing electric vehicles within the EU to Li-Cycle’s Germany Spoke. This signifies yet another partnership with a prominent global electric vehicle (EV) OEM, which it did not name.
“We are delighted to recycle lithium-ion batteries and manufacturing scrap sourced from across the EU as we work to expand our commercial reach and enhance value for our global EV OEM partners,” said Ajay Kochhar, Li-Cycle President/CEO.
“This partnership with a leading, premium EV manufacturer will serve as a vital source of recycling feedstock for our Germany Spoke, aiding our objective of offering a local and sustainable secondary supply of critical battery materials. We are excited to maintain our commitment to delivering high-quality services and products to our global partners as we develop a financially beneficial Spoke network.”
Established in 2016, and with major customers and partners around the world, Li-Cycle’s mission is to recover critical battery-grade materials to create a domestic closed-loop battery supply chain for a clean energy future. At its Spokes, or pre-processing facilities, it recycles battery manufacturing scrap and end-of-life batteries to produce black mass, a powder-like substance which contains a number of valuable metals, including lithium, nickel and cobalt.
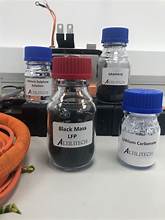
In related news, compatriot lithium-ion battery recycler Altilium says it has begun recycling lithium iron phosphate (LFP) batteries in the UK. The LFP batteries being recycled are from a global electric vehicle (EV) and energy storage systems (ESS) manufacturer.
The UK company claims its proprietary EcoCathode technology can recover more than 97% of the lithium and 99% of the graphite from end-of-life LFP batteries for reuse in new ones, not only strengthening the business model for recycling LFP batteries but also enabling automotive original equipment manufacturers (OEMs) to meet new regulatory targets and sustainability goals.
Altilium notes that most EVs use nickel cobalt manganese (NMC) batteries, but the rise of LFP presents new opportunities for recycling and resource conservation.
Altilium says it is addressing the challenge by recovering more of the lithium, which it describes as a high-value material, as well as recycling the graphite, which can be reused in the production of new anodes.
“The rise of LFP batteries presents both challenges and opportunities for recyclers,” says Altilium Chief Operating Officer Christian Marston. “At Altilium, we are pioneering solutions to ensure these batteries are not only recovered but play a key role in a UK circular battery economy. Our advanced EcoCathode technology allows us to efficiently extract lithium and graphite, making LFP recycling commercially viable and environmentally essential. By expanding our capabilities to process LFP alongside NMC batteries, we are strengthening the U.K.’s battery supply chain and supporting the transition to a cleaner, more sustainable transport sector.”
Altilium says it already is recycling NMC batteries from two UK-based automotive OEMs, as well as gigafactory production scrap, to produce modern high-nickel cathode active materials (CAM) at its ACT1 and ACT2 facilities.
The company’s recently opened ACT2 recycling plant in Plymouth, England, has the capacity to recover lithium and other battery metals from 300 kg of black mass per day, while its planned Teesside hub is designed to be one of the largest EV battery recycling facilities in Europe.
The company says the plant will have the capacity to process scrap from more than 150,000 EVs per year and has been designed to handle a mixed feed of battery chemistries, including LFP.
Subscribe to Get the Latest Updates from IMA Please click here
©2024 Injection Moulding Asia. All rights reserved.