Green materials: Suez, SK Geocentric and Loop to build PET recycling plant in France; Mitsubishi Gas Chemical to manufacture biomass PC with feedstock from Mitsui Chemicals
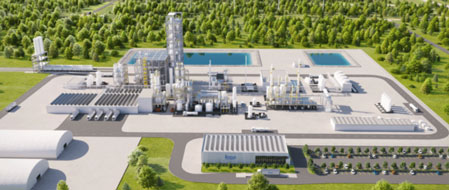
Technology firm Suez, Canada’s Loop Industries and South Korea’s SK Geo Centric have selected Saint-Avold, in France, as the site to manufacture virgin-quality PET plastic made from 100% recycled content and infinitely recyclable by leveraging the Infinite Loop process in a 70,000 tonnes/year facility with an investment of EUR450 million.
This international project, supported by the French Ministries of Industry and Ecology, the Grand Est region and the Saint-Avold Synergy region community, leverages the experience of SKGC in petrochemical processes, the expertise of Suez in the area of resource management and the depolymerisation technology of Loop.
The facility will manufacture 100% recycled and infinitely recyclable virgin-quality PET resin and has a planned capacity of 70,000 tonnes/year. This facility will help address the demand for recycled PET, which has continued to grow due to European regulations and requirements and will provide European-based global brands with a solution to their sustainability objectives of increasing the use of recycled content in their packaging and products.
The Saint-Avold Chemesis industrial platform is strategically situated in the heart of Europe and provides an efficient industrial and infrastructure network (access to energy notably via existing heat networks, road and rail logistics, suppliers, etc.) making it the optimum environment for the manufacturing facility. This project, which represents a projected overall investment of EUR450 million, will contribute to the sustainable revitalisation of the local industrial base and enable the direct creation of 200 new jobs.
Loop’s depolymerisation technology utilises low heat and no added pressure to upcycle low to no value feedstocks (that will otherwise go to incineration or landfill) into the highest purity, virgin-quality PET plastic. At full capacity, the facility could save over 255,000 tonnes of CO2 annually, when compared to virgin PET resin made from fossil fuels.
The entry flows of feedstock will be collected, sorted and prepared by SUEZ, leveraging its knowledge of the European plastics market, its partnerships with industrial players and its dense treatment infrastructure network coverage. By leveraging low value waste that is currently destined for landfill or incineration, this facility offers a solution to the global plastic waste challenge.
A local consultation process will be launched in the coming weeks to present the project to the general public. The three partners aim to start construction work in early 2025 with plant commissioning slated for 2027.
The facility in Europe is part of the global commercialisation strategy of Loop’s technology. Loop and SKGC are currently focused on the planning of the projected first Infinite Loop manufacturing facility in Ulsan, South Korea, which is expected to break ground in 2023.
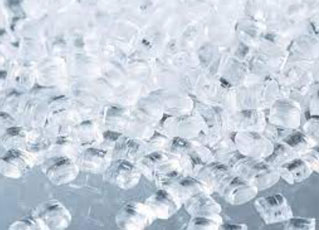
In other news, Mitsubishi Gas Chemical (MGC) as launched an initiative to manufacture biomass polycarbonate (PC) products. Mitsui Chemicals will provide biomass-derived bisphenol A (biomass BPA), which is scheduled to be developed under its BePLAYER brand, and MGC will use this as a monomer feedstock in the manufacture of its PC Iupilon.
In December 2021, Mitsui Chemicals was the first company in Japan to allocate derivatives and products (made with bio-based hydrocarbons as a raw material) using the mass balance method2 based on the ISCC PLUS certification system and is now selling biomass chemicals and resins. It has also begun to offer products in the biomass phenol chain, where it has traditionally been difficult to prepare biomass aromatic compounds taken directly from plant- derived raw materials. The company aims to have all seven products3 including BPA certified and on the market by March 2024. It will begin providing biomass BPA to MGC.
MGC will purchase ISCC PLUS certified biomass BPA from Mitsui Chemicals for the first time in Japan and will begin efforts to produce biomass PC at its Kashima Plant using the interface polymerisation method. MGC will utilise group company Kashima Polymer's pelletised products and functional compound products and group company MGC Filsheet's processing facilities for hard, highly transparent sheet products and film products for moulding to add functionality to biomass PC.
Furthermore, MGC is building an integrated supply chain for biomass PC products by marketing these products through the global sales networks of Mitsubishi Engineering-Plastics Corporation and Mitsubishi Gas Chemical Trading Co.
In addition, MGC's Kashima Plant and the MGC Group companies mentioned above are aiming to obtain ISCC PLUS certification by the end of this year. Up to now it has been challenging to procure biomass PC products for various fields including automotive, electricals and electronics, optics, OA, and semiconductors.
The ISCC PLUS certification will allow for these products to be supplied widely through the mass balance method. In addition, MGC is planning to use Circular Carbon Methanol together with biomass BPA to make the entire PC framework either CO2-derived or plant-derived. Meanwhile, overseas, MGC is planning to acquire ISCC PLUS certification at its PC material manufacturing bases, Thai Polycarbonate (based in Thailand) and MCC Process Plastics (Shanghai) (based in China).
(IMA)Subscribe to Get the Latest Updates from IMA Please click here
©2023 Injection Moulding Asia. All rights reserved.