Expansions: Teijin expanding composites footprint in China; Shin-Etsu to invest US$700 mn in silicone output in Japan
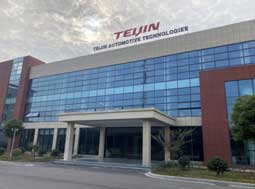
Teijin Automotive Technologies, the core company of the Teijin Group's automotive composites business, has begun commercial operation of a new composites manufacturing facility in the Wujin National Hi-Tech Industrial Zone based in Changzhou, Jiangsu province, China. The new facility boasts 39,000 sq m of work area. The company is also constructing a third plant in China, based in the Technological Development Zone of the Tiexi District in Shenyang, Liaoning province, and will begin operating this plant, with 13,000 sq m of work floor in the summer of 2023.
Teijin Automotive Technologies selected the Changzhou and Shenyang areas for its new plants due to their close proximity to the production facilities of several major European, US and Chinese automakers. Both plants will help to meet the growing demand for composites components due to the growth of the electric vehicle (EV) market in China. The two plants will significantly boost the company’s ability to supply lightweight, safe, energy-efficient and durable composite components, which are indispensable for environmentally friendly vehicles.
With the second plant’s startup and the third plant’s construction, Teijin Automotive Technologies says it is actively strengthening its position as a worldwide leader in automotive composite applications. Concurrently, the company is developing applications for advanced composite materials and processes to support its automotive customers’ challenges of achieving ambitious weight and CO2 reduction targets,and lower EV production costs. Teijin is targeting annual sales of US$2 billion for its automotive composite products business by 2030.
Teijin Automotive Technologies has been manufacturing automotive composites and glass-fiber sheet molding compounds (GF-SMC) in China since 2015, mainly for EV battery covers, battery shields, underbody shields, structural inner panels and exterior body panels.
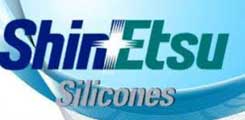
In other news, compatriot Japanese firm Shin-Etsu Chemical Co. will implement over US$700 million in facility investments for its silicones business, one of its main businesses, with the aim of further expanding and strengthening this business.
As a result of the announcement in September 2018 concerning its facility investment plan of ¥110 billion for its silicones business, Shin-Etsu Chemical increased its production capacity of silicone monomer, the intermediate material of silicones, at its two bases in Japan and Thailand by about 1.5 times, compared to the previous level.
Now, due to strong demand from customers mainly for advanced functional products, it is going to further increase production capacity in this business field as a result of this new facility investment. Shin-Etsu has already stated that it will strengthen the development of new silicone products and put the emphasis in its products structure on so-called specialty products.
This new facility investment plan is aimed at strengthening this business strategy, and the investment amount is expected to exceed ¥80 billion. By these means, it adds that it will “meet the vigorously increasing demand for these products, and at the same time, we will be able to strengthen our stable supply system”.
The new facility investments will increase its production capacity of highly diversified types of silicone fluids, resins and rubber end products. In addition, it will go forward with endeavours toward contributing to the reduction of the environmental impact and to the development of advanced technologies such as by introducing equipment for moulding silicone rubber that does not require post cure and by introducing trial production equipment for Micro LED-related materials, which will improve productivity and save energy.
This new series of facility investments will be implemented centring around plants in Japan, starting with our main plant, the Gunma Complex in Gunma Prefecture, as well as the Takefu Plant in Fukui Prefecture and the Naoetsu Plant in Niigata Prefecture. It aims to sequentially complete these capacity-expansion projects and begin operations by 2025.
(IMA)Subscribe to Get the Latest Updates from IMA Please click here
©2022 Injection Moulding Asia. All rights reserved.