Green tie-ups: Nextchem/Röhm tie-up for PMMA recycling in Italy; BASF/research partners collaborate on mechanical recycling of plastics
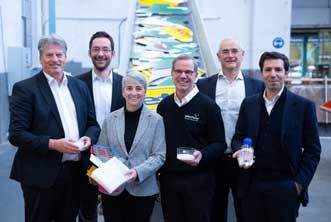
Italian firm Maire subsidiary Nextchem (Sustainable Technology Solutions), through its subsidiary MyRemono, has signed a Toll Manufacturing Agreement with PMMA manufacturer Röhm under which Röhm will supply PMMA scrap material feedstock to be processed and chemically transformed by MyRemono into ultra-pure monomers with virgin-like quality.
This initiative leverages on Nextchem's proprietary NXRe technology, a molten metal depolymerisation process for the continuous chemical recycling of PMMA. Röhm will also act as the off taker of recycled Methyl Methacrylate monomer (rMMA), to be reused for the manufacturing of new PMMA products in a fully circular process. The agreement provides for a processing fee to be paid by Röhm to MyRemono.
The initiative follows the establishment of a Europe-wide circularity network for the recycling of PMMA, which includes MyRemono, Röhm, Pekutherm and Polyvantis. Pekutherm will manage the logistics and sorting of PMMA materials, while Polyvantis will handle the mechanical recycling.
MyRemono will manage the chemical recycling of PMMA scrap material at its first-of-its-kind industrial-scale plant, currently being developed in Italy, with the support of the EU Innovation Fund. The plant is expected to be completed in 2026 with an initial processing capacity of about 5,000 tonnes/year of PMMA, an amount needed to produce approximately 10 million car taillights, demonstrating how significant volumes of recycled material can replace virgin resources in manufacturing.
Compared to the current virgin MMA production routes, the recycled MMA produced via NXRe PMMA is expected to feature a carbon footprint reduction of more than 90%. MyRemono’s overall investment for the technology development and scale-up, as well as for the construction of the first industrial-scale plant, amounts to EUR15 million, mainly funded by a bank loan and the EUR4 million EU Innovation Fund grant.
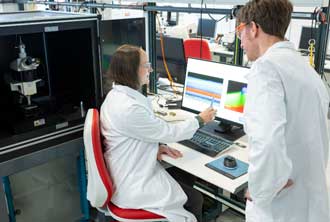
In other news, German chemicals firm BASF has teamed up with Endress+Hauser and TechnoCompound as well as the Universities of Bayreuth and Jena to study how the mechanical recycling of plastics can be improved.
With funding from the German Federal Ministry of Education and Research (BMBF), the SpecReK project aims to reliably and precisely identify the composition of plastic waste during the recycling process and thus improve the quality of recycled plastics. This will be achieved by combining measuring techniques with artificial intelligence (AI).
The researchers are using spectroscopic methods which interpret how the material interacts with light to gain information about the chemical structure of the recycled plastics. The project partners want to use this data to determine in real time during processing which plastic grades, additives and contaminants are contained in the material.
In a subsequent step, an AI algorithm will recognise patterns in the measurement data and recommend which additional components should be added or how the recycling process should be adapted to improve the quality of the recycled plastic output.
“We do not currently have the necessary analysis tools to determine during processing exactly which components are contained in the mechanically recycled plastics,” explained Dr Bernhard von Vacano, head of the Plastics Circularity research program at BASF. “This information is needed, however, to evaluate and improve the quality of waste plastics. This will enable us to use more mechanically recycled plastics to produce high-quality products and to make recycling processes more efficient and sustainable,” said von Vacano.
At present, most of the plastic waste that is sent for recycling is mechanically recycled. The waste is collected, sorted, crushed, cleaned and then melted. Depending on the input material and the degree of sorting, this melted material can contain different types of plastics, additives and contaminants. Therefore, the quality of the recycled output often varies and is not always sufficient to be transformed back into high-value plastic products.
“With the increasing demand for high-quality recycled materials, and given the current legal framework, it will be crucial to perfectly understand the material properties and composition of mechanically recycled plastic waste and to optimise the process,” von Vacano said.
In this joint project, BASF is cooperating with Endress+Hauser, TechnoCompound, the University of Bayreuth and Friedrich Schiller University Jena. The total project volume is EUR2.2 million, with two-thirds financed by BMBF funds from its quantum systems research program and one-third financed by the project partners.
In cases where mechanical recycling of plastic waste is not technologically feasible or too complex, plastics can also be brought back into the material loop via chemical recycling. Both recycling processes – chemical and mechanical – are important for a functioning circular economy and can complement each other.
That is why BASF says it is working to continuously improve both types of recycling.
Subscribe to Get the Latest Updates from IMA Please click here
©2024 Injection Moulding Asia. All rights reserved.