Green materials: Emirates Biotech opts for Sulzer technology for PLA facility; Graphjet opens sustainable palm oil waste-to-graphite facility in Malaysia
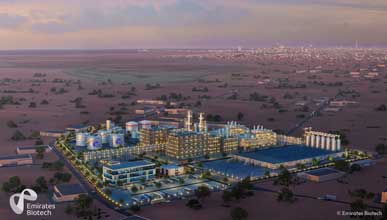
Emirates Biotech has selected Swiss chemical firm Sulzer Chemtech as the technology provider for its upcoming polylactic acid (PLA) production plant in the UAE. The facility will be constructed in two phases, each with an annual capacity of 80,000 tonnes, resulting in a total production capacity of 160,000 tonnes/year.
Located in the UAE, construction is set to commence in 2025, with the plant expected to be operational by early 2028. The facility will use lactic acid as its feedstock to produce PLA.
Once completed, it will be the largest PLA production facility in the world, says Emirates Biotech. It adds that this volume of bioplastic material is enough to replace approximately 3.2 billion plastic bottles and will reduce CO2 emissions by over 300,000 tonnes/year.
PLA offers a sustainable alternative to traditional plastics. It is widely used in applications such as packaging, disposable utensils, helping to reduce reliance on single-use plastics across the globe.
Emirates Biotech adds it will leverage Sulzer’s licensed PLA technology to manage all production steps from a single location, including lactide production, purification and polymerisation. The facility will also use a plant-based feedstock to produce high-quality PLA bioplastics at scale, positioning the Middle East as a key player in the bioplastics industry.
With over two centuries of industry experience and a strong track record in the bioplastics sector, Sulzer’s licensed PLA technology is already in use at most PLA facilities worldwide. This new development strengthens Sulzer’s commitment to supporting global industry in adopting circular manufacturing and building a more prosperous and sustainable society.
As the global demand for PLA continues to rise, driven by environmental concerns and the shift towards sustainable materials, this facility will position the Middle East as a key player in the bioplastics industry, supporting regional and global efforts to combat plastic pollution.
In other news, carbon materials supplier Graphjet Technology, which was set up in 2019 to produce artificial graphite from biomass waste residues from palm oil, has started up its first commercial-scale green graphite facility in Subang Jaya, Selangor, Malaysia. It says that the facility is the world’s first commercial-scale plant capable of recycling palm kernel shells, a highly abundant agricultural waste byproduct in Malaysia, to produce battery-grade graphite.
The new facility has the capacity to recycle up to 9,000 tonnes/year of palm kernel shells, producing up to 3,000 tonnes/year of graphite. This level of production is sufficient to support battery production for approximately 40,000 electric vehicles (EVs) per year.
With a footprint exceeding 91,000 sq ft, Graphjet’s facility will support a local workforce of 200 jobs.
Graphjet adds it has received its first shipment of palm kernel shells and has begun shipping green graphite product samples to its customers. Additionally, the company plans to produce hard carbon at the facility to provide feedstock for its planned green graphite facility in Nevada.
The Graphjet team has achieved a monumental step towards the execution of our strategy and vision to become a reliable supplier of green graphite globally,” said Aiden Lee, CEO/Co-Founder of Graphjet.
“With this facility online, Graphjet is now the primary player in green graphite production outside of China, as the company has the largest production capacity ex-China. This facility, which is the first graphite facility to commence operations outside of China, demonstrates our ability to leverage our technology at scale, and we are proud to commence commercial operations at the world’s largest green graphite facility of its kind. This facility will provide us with an ability to generate revenue by FY 2025, support our valued customers, and establish a strong foundation for a successful launch in the United States in Nevada.”
Graphjet’s facility utilises the company’s patented technology to produce green graphite directly from palm kernel shells. This technology reduces the company’s operational carbon footprint by up to 83% and reduces costs by up to 80% compared to traditional processes.
It adds that per kg of graphite produced, only 2.95 kg C02 is emitted, compared to 16.8 kg C02 emissions and 17 kg C02 emissions from natural and synthetic graphite production, respectively, in China.
Graphjet’s technology is expected to have the lowest carbon footprint of any graphite production process in the world.
Subscribe to Get the Latest Updates from IMA Please click here
©2024 Injection Moulding Asia. All rights reserved.