Automotive Industry: Collaborations bring results for circular economy
LyondellBasell/Audi tie-up for recycled material seatbelt buckle covers
Chemical firm LyondellBasell and car maker Audi have collaborated on the development of a closed- loop process for mixed automotive plastic waste, the companies say. The project, part of Audi’s PlasticLoop project, will see the car maker installing plastic seatbelt buckle covers in its Q8 e-tron model that are made using chemically recycled plastic from LyondellBasell.
It is the first time the company is installing safety components made in this way from a stream of material which to date has been mostly only suitable for energy recovery.
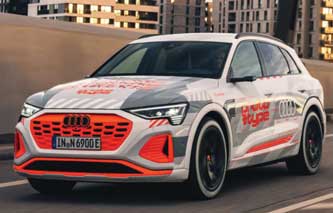
Plastic components from customer vehicles that can no longer be repaired are dismantled, shredded, and processed by chemical recycler SynCycle - a joint project of the Austrian companies Next Generation Group and BDI-BioEnergy International - into pyrolysis oil.
The pyrolysis oil is then used as a raw material in LyondellBasell’s manufacturing process for the production of new plastics, replacing virgin fossil feedstocks. The recycled content is attributed to the Audi product via a mass balance approach.
Materials produced from pyrolysis oil are of the same high quality as virgin materials and have the same properties. Chemical recycling offers an alternative to energy recovery and complements mechanical recycling.
Citroën/BASF unveil all-electric concept car oli
Meanwhile, Citroën and German materials firm BASF have unveiled their all-electric concept car oli [all-ë], a manifesto to how much can be saved by reducing weight and resource usage.
With speed limited to 110 km/hour and acceleration close to the classic 2CV model, the concept car gains a wider range and significantly improved battery lifespan.
Various components have been radically reinterpreted and constructed by using materials in a different context. For example, the complete backrest is made of a flexible 3D-printed plastic material (Ultrasint TPU88A).
The open lattice structure provides natural air flow, replacing all ventilators in the seat. For this, as well as to produce about 20 parts the competence of the 3D printing service office, Sculpteo in France, a brand of BASF, was used.
Another striking feature is that many of the new components are designed and manufactured from materials from the same chemical product family. Bonded and welded components made from different materials are a challenge in mechanical recycling. For this reason, the designers created as many components as possible from a single material.
This principle of simplicity was also implemented during production. With the driver and front passenger doors being identical, this saves on pressing tools and reduces complexity. The same applies to all wheel arches and bumpers.
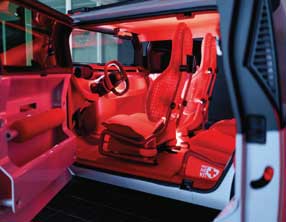
The colour of the body perfectly conveys the concept of the car. At first glance it seems to be a pure white colour, but mica particles have been added to emphasise the shape of the car. In contrast to the exterior, the materials of the interior – such as the seats and the flooring – have been coated with an intense orange colour.
Many BASF automotive solutions have been used such as Infinergy, an expanded thermoplastic polyurethane (TPU), also used in running shoes and sports flooring, can be found in the rear armrests and the interior floor of the car. The material provides a pleasant yet stable surface in armrests and floors. Plus, it dampens noise and vibrations. Additionally, a special coating is applied to ensure an extra long life span.
The water-based NovaCoat-P coating is ideal for protecting soft substrates against abrasion, UV radiation, dirt, and chemicals. And because the flooring is waterproof, it can be easily cleaned with water. This is where the integrated plugs made of Elastollan come in handy, as they can be removed to drain water and dirt.
The weight of the vehicle exterior was also considerably reduced, while at the same time increasing stability and durability. The hood, roof, and trunk are made of panels combining the Elastoflex PU system and the Elastocoat spray paint system. Thanks to the honeycomb sandwich structure, these panels are so stable that you can even stand on them.
Used for coating the car body, R-M AGILIS water- based coating is another BASF product that provides sustainability with its low content of VOCs.
BASF CathoGuard 800 electrocoat, which protects the battery housing from corrosion, contributes to further resource savings. It stands out for its high performance and eco-friendliness as it is tin/HAPs-free and with low solvent content.
(IMA)Subscribe to Get the Latest Updates from IMA Please click here
©2022 Injection Moulding Asia. All rights reserved.