Expansions: Mitsui to bolster output of elastomers in Singapore; LG Chem to boost CNT supply for EVs with fourth plant in South Korea
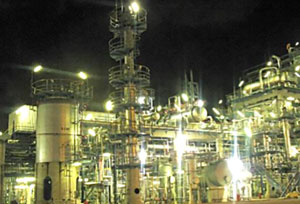
Japanese chemical firm Mitsui Chemicals has announced plans to bolster capacity at its Singapore-based wholly owned subsidiary Mitsui Elastomers Singapore by building a new plant to produce the high-performance elastomer Tafmer in Jurong Island. It will have a capacity of 120,000 tonnes/year and be scheduled for running in 2024. The capacity of the existing facility is 225,000 tonnes/year.
Tafmer is used both as a soft moulding material and as a resin modifier that is said to improve resin properties. Its flexibility and lightness have resulted in the elastomer being used across a wide range of fields, including solar cell components, packaging materials, engineering plastic modifiers, sports shoes and automotive parts.
Demand for the elastomer is said to be strong amid robust global economic growth, and is expected to rise further on the back of efforts to achieve a circular economy and step up the introduction of clean energy. Via the supply of Tafmer, which meets these needs, Mitsui Chemicals says it aims to become a global solutions company that leads change and contributes to sustainability.
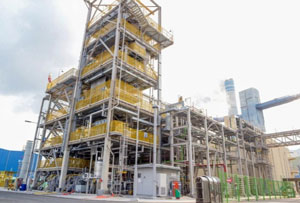
In other news, South Korea’s LG Chem is expanding its investment in carbon nanotubes (CNTs) with the construction of what it says will be the world’s largest single-line CNT manufacturing plant. The new plant is part of LG Chem’s initiative to gain a more competitive edge in the rapidly growing global CNT market focused on electric vehicle (EV) battery materials. The new facility will be LG Chem’s fourth CNT plant, following Plant 3 which started construction early this year and Plant 2 which has been operational since last year. The new plant will be built in LG Chem’s Daesan Complex, with construction commencing in the first half of next year and operation beginning in the second half of 2024.
The 3,200 tonnes of CNT produced at Plant 4 will contribute to LG Chem’s total carbon nanotube production capacity of 6,100 tonnes across four plants. LG Chem has been operating CNT plants since 2017, starting with 500-tonne production at its CNT Plant 1, and has been building new plants every year since 2020 to meet growing demand.
Thanks to the company’s fluidised-bed reactor technology, each production line at all four of LG Chem’s CNT plants can produce up to 600 tonnes/year, said to be the highest single-line capacity in the world. Production capacity per capita at LG Chem’s Plant 4 is expected to be 20% higher than its other plants due to efficiencies related to improved reactor stability and process automation.
LG Chem also says the CNTs produced at the plants are also high-quality due to its self-developed cobalt-based catalysts that help lower magnetic impurities, which may negatively affect battery quality.
CNT is a next-generation material offering the equivalent level of electricity and thermal conductivity as copper and diamond and 100 times the strength of steel. Due to its excellent properties that surpass existing materials, CNT has an infinite range of applications in batteries, semiconductor wafer trays, automotive components, and surface heating elements. The global CNT conductive additive market is expected to grow by 30% to US$2.3 billion contributing to the demand of CNT increasing from 5,000 tonnes in 2021 to 70,000 tonnes by 2030.
CNTs produced by LG Chem will be supplied as conductive additives to battery makers such as LG Energy Solution, the current leader in the global EV battery market, with plans for usage to be expanded to a broader range of industries.
When utilised as a conductive additive, CNT demonstrates 10% more conductivity than carbon black, allowing battery makers to use 30% less conductive additives. The available space can then be filled with cathodes for higher capacity and longer lifespan without increasing the overall size of the battery. Given this, CNTs are also being considered attractive futuristic conductive additives for even anodes and next-generation batteries such as lithium-sulphur and solid-state batteries.
(IMA)Subscribe to Get the Latest Updates from IMA Please click here
©2022 Injection Moulding Asia. All rights reserved.