Recycling tie-ups: Eastman, USAMP and PADNOS in recycling study for auto market; DSM/Sabic in recycled Dyneema effort
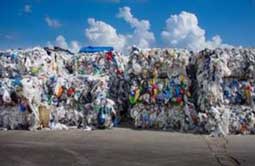
US materials firm Eastman has entered into a collaboration with the United States Automotive Materials Partnership and family-owned automotive recycler PADNOS for a concept feasibility study to demonstrate a closed-loop project to recycle automotive-industry mixed plastic waste in the automotive supply chain. USAMP is a subsidiary of the United States Council for Automotive Research (USCAR).
When automobiles are at the end of their life, metals, tyres, and glass account for 80%–90% of the materials that can be recycled through traditional mechanical recycling streams. The other 10%–20%, referred to as automotive shedder residue (ASR), consists of mixed plastic and other non-recycled materials that currently end up in landfills or are recovered through waste-to-energy technologies. Under this initiative PADNOS will use ASR as a sustainable feedstock for Eastman's molecular recycling process, creating a truly circular solution.
The study will also assess how well Eastman's carbon renewal technology (CRT), one of Eastman's two molecular recycling technologies, breaks down the plastic-rich fraction of ASR into molecular building blocks. By recycling these complex plastics in CRT, Eastman can replace fossil-based feedstock and create polymers without compromising performance for use in new automotive applications.
USAMP sees the potential for energy savings and reduced overall greenhouse gas emissions while eliminating a significant fraction of the 5-7 million tonnes/year of ASR generated in the US from landfills.
"This 12-month automotive recycling project with Eastman and PADNOS is part of USAMP's broad materials research and sustainability program," said Steve Zimmer, Executive Director of USCAR. "Programs like this are critical to establishing a cost-effective pathway for addressing challenges associated with the consumption of ASR back into automotive parts to enable true industry circularity."
Steve Crawford, executive vice president, chief technology, and sustainability officer for Eastman, cited this as a prime example of how collaboration across the value chain is essential to making material circularity mainstream.
"Our molecular recycling technologies are recycling complex plastic waste at commercial scale now, but technologies alone won't build a circular economy — it takes work across the value chain by multiple players who are determined to deliver sustainable solutions," Crawford said. "That's why this project is so exciting. The member companies of USCAR — Ford, General Motors and Stellantis — are accelerating their approach to designing for more sustainable end-of-life solutions, and this project can be a catalyst for circularity within the automotive value stream that addresses both the climate and waste plastic issues and reshapes what we thought was possible."
PADNOS is a family-owned and operated recycling company located in Michigan and Indiana, USA with national and global reach. With diverse processing capabilities, PADNOS is able to collaborate and innovate with customers to provide sustainable scrap solutions.
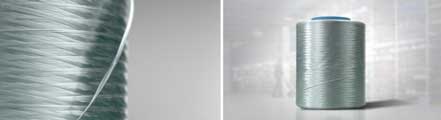
Meanwhile in other news, Dutch materials firm DSM is collaborating with chemical firm Sabic to create recycled-based Dyneema. Through a joint pilot with multiple CirculariTeam members, the manufacturing and usage of Dyneema using mixed plastic waste as feedstock (via mass balance approach) will be successfully demonstrated. It is an important step toward the future goal of fully closing the loop by delivering Dyneema made from ultra-high molecular weight polyethylene (UHMwPE) waste. This collaboration underlines DSM’s and SABIC’s efforts to accelerate a circular economy for materials.
By working together with members of CirculariTeam, DSM will produce recycled-based Dyneema made using Sabic’s certified circular ethylene as a pilot project in both a sailing rope and a pelagic trawl net application. The circular ethylene, from Sabic’s Trucircle portfolio, uses mixed plastic waste as feedstock (mass balance approach), which not only contributes to preventing valuable plastic from becoming waste and the avoidance of carbon emissions compared to incineration, but it will also help preserve fossil resources. These pilots are an important early-stage milestone in the journey toward making fully circular Dyneema from HMPE post-production and post-consumer waste.
Jan-Lodewijk Lindemulder, President DSM Protective Materials: “This achievement is a key milestone on the journey toward our goal of delivering a fully circular Dyneema. By working with partners from across the value chain, we are able to significantly reduce the environmental impact of the world’s strongest fibre – and we will continue to explore ways of reducing and eliminating waste across the entire product lifecycle.”
Mark Vester, Circular Economy Leader at Sabic: “This is another important step closer to closing the loop on Dyneema. Moving forward, through our Trucircle solutions and beyond, we will continue to make every effort to deliver a more sustainable value chain and economy.”
Jon Mitchell, Managing Director at Marlow Ropes: “We are able to create products that not only deliver superlative functional performance but also have a lower environmental impact. Our products are trialled and tested by professional offshore sailing teams including 11th Hour Racing Team, a proud partner of ours at Marlow, with whom we share a progressive approach to seeking sustainable solutions: no more business as usual."
Klaus Walther, Managing Director at Gleistein: “We’re proud that our ropes can be produced from what once was typical household plastic waste. This is an important stepping stone towards becoming circular. It will enable our customer Maritiem BV to further develop high-tech fishing gear whilst contributing to the circular economy. Not to forget Cornelis Vrolijk Fishing Company, who again illustrate their commitment to Corporate Social Responsibility by introducing this concept in fishery.”
(IMA)Subscribe to Get the Latest Updates from IMA Please click here
©2021 Injection Moulding Asia. All rights reserved.