Green materials: Emmi, Borealis, Greiner partner in recycled PP cups; Hexpol’s recycled TPEs for auto sector
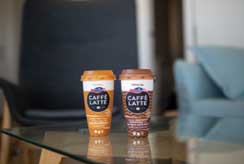
Emmi, a ready to drink iced coffee brand in Europe, has started to incorporate chemically recycled polypropylene (PP) into its packaging. The cups are produced by Greiner Packaging and the chemically recycled material (30% Borcycle C) comes from Austrian polyolefins supplier Borealis.
Emmi, Switzerland’s largest milk processor, has the stated goal to make all of its packaging 100% recyclable and is committed to various measures to promote circularity such as packaging that contains at least 30% recyclate by 2027. Focusing on recyclable packaging and the use of recycled materials, Emmi is taking a first step with its CAFFÈ LATTE brand.
From September 2021, Emmi says it will use at least 100 tonnes/year of plastic based on the recycled material. Chemical recycling renews plastic back to plastic creating recycled materials with a level of purity equivalent to fossil-fuel based PP and hence, fit for protective, food-safe and other demanding applications.
In the future, depending on the availability of suitable material, the amount of recycled plastic in Emmi packaging is to be further increased, it adds.
The new technology to recover PP is currently still in its infancy, where Greiner Packaging and Borealis are leading the way. Only limited quantities of chemically recycled PP are currently available, and Emmi is one of only a few food manufacturers to have secured a share of the chemically recycled PP plastic through its early commitment and long-standing collaboration with the development companies.
The chemically recycled material used for Emmi CAFFÈ LATTE cup consists entirely and solely of ISCC (International Sustainability & Carbon Certification) material, on a mass balance basis. Mass balance is a methodology that makes it possible to track the amount and sustainability characteristics of circular and/or bio-based content in the value chain and through each step of the process. This provides transparency ultimately also to the consumers, enabling them to know that the product they are buying is based on this renewable material.
Recovering plastic from plastic packaging: Chemical recycling enables chemical raw materials to be recovered from plastic waste that is otherwise difficult to recycle mechanically – an important part of the solution for increasing recycling rates, and for preventing plastic waste from being landfilled or incinerated and thus keeping it in the cycle as a raw material. These materials have the same properties as plastics from traditional production (“virgin plastics”) and are approved for use with food.
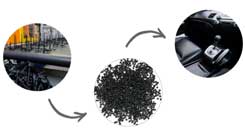
Meanwhile in other news, Swedish TPE maker Hexpol has expanded its range of thermoplastic elastomer (TPE) materials with recycled content. The new Dryflex Circular TPE grades have been tested for odour and emissions performance in automotive interiors.
Dryflex Circular TPEs were developed to support the shift from finite fossil-based virgin materials. They were launched in 2019. Recycled polymers from various sources, including Post-Consumer (PCR) and Post-Industrial (PIR), are incorporated into the Dryflex Circular TPEs. They can also be recycled in closed-loop systems at the end of life.
An important aspect of automotive interior parts is their emission behaviour regarding odour and volatile substances. The exact specifications and requirements vary depending on application and OEM. But generally, the material odour must not be disturbing even at higher temperatures (e.g., 80°C). A representative Dryflex Circular TPE grade, a 65 Shore A material for inlay mats with a recyclate content of 20%, showed a very low amount of VOC (60 μg/g) and FOG (594 μg/g).
The TPE was tested at an external accredited laboratory and shown to have almost no odour (grade 2.0 according to VDA 270, B3). The mechanical properties fulfil automotive requirements, and colourability is possible. The material is currently being approved by a German car manufacturer.
The recyclate sources are diverted from waste streams during post-industrial manufacturing processes. They originate from injection moulding sprues or edge trims in extrusions. The chosen recyclates were selected due to their high levels of consistency and purity.
With consideration of transportation and energy impacts, the recyclates are sourced in Europe. Dryflex Circular TPEs are produced at Hexpol's European sites, which use 100% renewable electricity.
The new Dryflex Circular TPEs can be used in various automotive interior applications such as inlay mats, cup holders, sealing lips and HVAC parts.
(IMA)Subscribe to Get the Latest Updates from IMA Please click here
©2021 Injection Moulding Asia. All rights reserved.