Recycling: Trinseo/MagREEsource to integrate recycling of PC/rare earth magnets; Asahi Kasei/Nobian in jv for recycling rare metals used in electrolysers
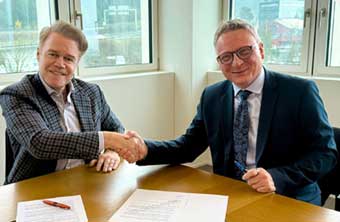
Materials firm Trinseo and Swiss firm MagREEsource are exploring collaborative opportunities for recycling solutions by combining Trinseo’s proprietary polymer dissolution recycling capabilities with MagREEsource’s proprietary rare earth magnets recycling model. A Memorandum of Understanding (MOU) was signed recently to signify the collaboration.
Trinseo’s technology uses a physical recycling process that requires minimal sorting, extracting polycarbonate (PC) from entire end-of-life products, even in mixed or contaminated materials. The extracted PC is recycled into new materials with over 70% cradle-to-gate estimated product carbon footprint reduction compared to its virgin counterpart, while non-PC components, including magnets, remain for further recycling.
This two-stage process is particularly effective for consumer and industrial products made primarily of PC and containing magnetic systems, especially neodymium (NdFeB) magnets vital for low-carbon applications such as wind turbines, electric vehicle motors, and automation.
“The technologies from Trinseo and MagREEsource are complementary, and we believe that value chain collaborations are fundamental to advancing sustainability,” said Han Hendriks, Chief Technology and Sustainability Officer at Trinseo. “This partnership shows the shared vision of both companies.”
With its circular magnet-to-magnet model MagREEsource is dedicated to recovering end-of-life rare-earth magnets and manufacturing new low-carbon magnets for demanding applications like windmills, electrical vehicles, aeronautics or medical to meet EU market demand.
“Our collaboration has potential to benefit the value chain as byproducts of Trinseo’s dissolution process could serve as input materials for our process. Byproduct magnets are an important part of supply for our MagFactory (1,000 tonnes/year of magnets production), construction of which is anticipated to begin at the end of 2026,” said Erick Petit, President/co-founder at MagREEsource.
“Given the European Union’s ambitious sustainability plans, these innovations from MagREEsource and Trinseo contribute to advancing the EU industry’s progress toward sustainability targets by enabling increased material recovery and emissions reduction,” he concluded.
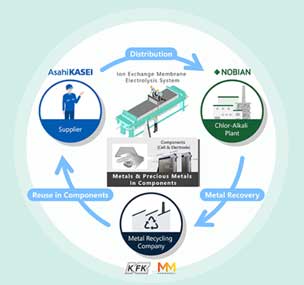
In related news, chemicals firm Asahi Kasei has started a joint demonstration with Nobian, Furuya Metal, and Mastermelt on the recycling of metals, including precious metals, used in the cells and electrodes incorporated in electrolysers used for the production of caustic soda.
Through this initiative started in February 2025, the partners will work towards building a recycling ecosystem for valuable metals in the chlor-alkali industry.
For nearly five decades, Asahi Kasei has been involved the field of chlor-alkali electrolysis for the production of caustic soda and chlorine. The company manufactures and supplies ion-exchange membranes, electrolysis cells, electrodes, and operation expertise for electrolyser plants.
Electrolysers apply an electric current that is used to split salt water (brine) into chlorine, hydrogen, and caustic soda, which are then used in a broad variety of chemical products.
Precious metals such as iridium and ruthenium are used to produce electrodes and other components for electrolysis systems.
With increasing global demand for these materials, Asahi Kasei has been advancing initiatives with partners to ensure a stable and secure supply of these metals. One such example is a demonstration project of an electrolysis cell rental service in Europe.
Running since 2023 in collaboration with Nobian, a manufacturer of caustic soda and other essential chemicals, this project focuses on the reuse of precious metals.
Asahi Kasei’s joint recycling project with Nobian, as well as with recycling specialists Furuya Metal and Mastermelt, aims to establish a recycling process inside the chlor-alkali industry that refines metals from cells and electrodes that have reached the end of their service life and reuses them as raw materials for the production of new components within the industry.
It is expected that this may also be applied to components of Asahi Kasei’s electrolysis system for producing green hydrogen using clean energy.
In this project, Asahi Kasei will first collect end-of-life electrodes from Nobian and provide them to Mastermelt and Furuya Metal which will perform the removal of the catalyst from the electrodes, preparation of the material for the next process step, and the extraction and purification of precious metals from the catalyst.
In the final step, Asahi Kasei uses the precious metals for a new catalyst, which is then utilised for the coating of electrodes. By using these recycled catalytic electrodes, Nobian will conduct brine electrolysis, thereby enabling resource recycling in the production of caustic soda and chlorine.
This announcement follows Asahi Kasei’s launch of the AlkaNexus brand in late 2024, which is designed to be a one-stop solution for the chlor-alkali industry, integrating advanced services in data analysis, plant operations optimisation, and membranes.
Owned by Carlyle Group and GIC, Nobian specialises in the production of salt, essential chemicals and storage caverns, and operates sites in the Netherlands, Germany, and Denmark. It supplies high-purity salt, chlor-alkali, chloromethanes, and hydrogen for energy transition products.
Furuya Metal, established in 1968, is a manufacturer that processes platinum group metals (PGMs) into industrial products, while Mastermelt has 25 years of experience in the recycling of precious metals from the chlor-alkali industry. It has sites in the UK, Germany, Singapore, and the US, and highly specialised facilities specifically for recovery of precious metals from electrodes.
Subscribe to Get the Latest Updates from IMA Please click here
©2025 Injection Moulding Asia. All rights reserved.