Liquid Silicone Rubber Moulding: LSR stretches to innovations in automotive and medical sectors
Liquid silicone rubber (LSR) is making a clear impact in automotive and medical applications, with the market responding favourably, says Angelica Buan in this report.
Global growth of LSR demand
Global demand for liquid silicone rubber (LSR) is reaching new heights as industries seek high-performance materials for medical devices, automotive components, consumer goods, and more.
According to a report by Persistence Market Research, the LSR market is projected to grow at CAGR of 8.4% through 2031. The automotive sector remains the largest end-user, driven by the need for durable, highperformance components, while the medical segment follows due to LSR’s biocompatibility, sterilisability, thermal stability, and flexibility, among other features.
To keep pace with rising demand, material solutions providers are scaling development and production, introducing advanced LSR formulations that enhance durability, flexibility, and precision. As innovation continues, new applications for this versatile material are emerging across industries.
LSR development spurs automotive market growth
Leading companies in the LSR sector are expanding production, developing new products, and adopting sustainable practices, especially for automotive applications.
German chemical company Wacker Chemie has further strengthened its foothold in the Asian market with new specialty silicone production facilities in Japan and South Korea.
The plants, located in Tsukuba, Japan, and Jincheon, South Korea, will support growing demand, particularly in the automotive and construction industries and represent an investment in the double-digit million-euro range.
Wacker stated that the additional capacity will help meet increasing demand, particularly in Asia, which already accounts for over 40% of Wacker’s sales, with Japan and South Korea playing a key role.
The Tsukuba site is focused on supporting the automotive industry, especially electromobility. It includes a production line for silicone-based thermal interface materials (TIMs), elastomers modified with additives and fillers to enhance thermal conductivity. These materials serve as gap fillers in electronics, improving heat management for components such as electric vehicle (EV) batteries. By embedding batteries in silicone encapsulants, heat dissipation is controlled, preventing overheating and improving safety
Japanese automotive suppliers are actively investing in electromobility, aiming to refine battery-powered vehicle designs. Silicones are utilised in hybrid cable systems, thermal management solutions, potting for power electronics, and battery safety enhancements. The new production line in Japan will allow Wacker to meet regional demand for these advanced materials.
At the same time, Wacker has expanded capacity at its Jincheon site in South Korea. The company has been producing silicone sealants for construction there since 2010, later adding specialty silicones, LSR, and silicone elastomers for automotive and electrical applications in 2012.
Durable adhesion and coating solutions for mobility sector
In line with industry advancements, US chemical firm Dow’s Silastic SA 994X LSR series, which it debuted in 2022, continues to support the development of technologies for the mobility and transportation sector, it adds.
The Silastic series consists of primerless, self-adhesive, general-purpose, and self-lubricating LSRs with a one-to-one mix ratio, designed for two-component injection moulding with thermoplastic substrates such as PBT and PA.
Furthermore, the series works for automotive uses like connector seals, battery vent gaskets, and radiator gasket seals in electric and hybrid vehicles, as well as environmental protection seals for lidar and radar housings in autonomous vehicles. It provides durable adhesion under heat and humidity, achieves full bond strength instantly, maintains a 12-month shelf life, and bonds strongly to various plastics and metals without additional heat treatment.
Critical material for reliable insulation
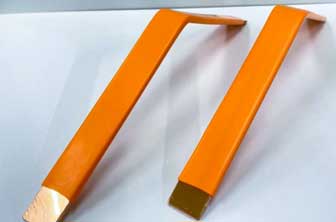
In another development, Japanese chemical company ShinEtsu Chemical Co has introduced ST-OR heat-shrinkable silicone rubber tubing, marking an industry first for busbar insulation.
Busbars, typically made of copper or aluminium and used in switchboards, control panels, and electric and hybrid vehicles, require reliable insulation due to the high voltages and currents involved.
The ST-OR tubing meets these demands with high electrical insulation properties, featuring a dielectric strength of 28 kV/mm. It remains stable in extreme temperatures ranging from −40°C to +200°C. The tubing’s bright orange outer surface also makes it a high-visibility alternative to high-voltage cables. Unlike other insulation materials, it retains the flexibility characteristic of silicone rubber, even after the heatshrinking process.
For applications requiring both electrical insulation and thermal conductivity, Shin-Etsu has developed the ST-TC-1, offering a thermal conductivity of 1.0 W/m·K. This version ensures efficient heat transfer while covering heating components.
A major advantage of this tubing is its ease of application. When heated, it shrinks around the busbar, creating a secure insulating layer without complex installation procedures. Moreover, this innovation enhances the reliability of power distribution systems while reducing time and labour costs.
Gecko-inspired material for patient safety
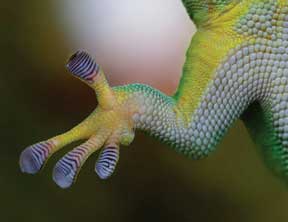
Innovations in LSR are improving healthcare by enhancing medical devices, prosthetics, and patient safety solutions. Researchers at the ACS Applied Materials & Interfaces, funded by the Foundation for Science and Technology in Portugal, have developed a geckoinspired slip-resistant material that could reduce injuries from slips and falls. The new polymer, made from LSR enhanced with zirconia nanoparticles, mimics the adhesive properties of gecko footpads and improves traction on slippery surfaces. Scientists believe it could be incorporated into shoe soles to enhance grip.
Many existing anti-slip soles, often made from natural rubber, struggle to maintain traction, specifically in wet conditions. Inspired by geckos, whose footpads use hydrophilic capillary-enhanced adhesion to grip slick surfaces, researchers sought to replicate this effect in a synthetic material.
The LSR/zirconia nanoparticles material, to attract water molecules, is rolled into a thin film, hardened with heat, and laser-etched with grooves to expose the hydrophilic particles. This structure allowed the polymer to create suction, similar to gecko footpads, making it highly slip-resistant.
Tests on different versions of the material, with zirconia concentrations ranging from 1% to 9%, showed that the 3% and 5% formulations provided the best grip. The researchers believe this technology could also have medical applications, such as in electronic and artificial skin, where polymers interact with fluid layers between surfaces.
Subscribe to Get the Latest Updates from IMA Please click here
©2025 Injection Moulding Asia. All rights reserved.