Recycling: Denso/partners team up for automotive recycling process; Mura partners with Belgian university to explore chemical recycling
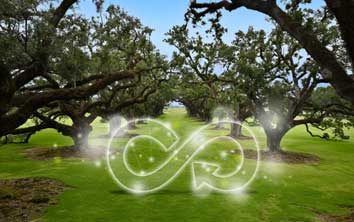
Denso Corporation and 16 partners are participating in an automotive circular economy project, supported by Ministry of the Environment, Japan. The companies have been selected for an industry-government-academia collaborative project aiming to expand the recycle content for automobiles. The project started in early March and is scheduled to conclude by the end of January 2025.
Project participants include Rever Corporation, DIC Corporation, UACJ Corporation, Kaneshiro Sangyou, Kyushu Metal Industry, Sumitomo Chemical Company, Daido Steel Co, Toray Industries, Toyoda Gosei Co, Toyota Boshoku, Nomura Research Institute, Furukawa Electric Co, Matec Inc, Mitsui Chemicals, Waseda University, and others.
In recent years, the automotive industry has sought to transition to a circular economy to achieve a more sustainable society. In the effort, it is necessary to significantly expand the use of recycled materials in automotive products, helping reduce the need for freshly cultivated natural resources.
Even so, current global processes often involve shredding ELVs and separating the remaining materials for use in recycled products, a process that can make acquiring high-purity material a challenge. Further compounding the issue is a lack of shared standards between the manufacturing and recycling industries.
Moreover, the recycling industry responsible for ELV processing faces business challenges such as severe labour shortages and the need to optimise work environments. Addressing these challenges requires a shift towards new processing methods for ELVs that not only solve these issues but also ensure the quality and quantity of recycled materials.
In this project, participating companies such as ELV dismantling and shredding operators, dismantling system providers, material manufacturers, automotive parts manufacturers, and research institutions are collaborating to realise a new ELV processing method based on automated sophisticated dismantling and conduct a technology demonstration of an integrated process.
Through this demonstration, the group will identify the challenges involved in implementing this integrated ecosystem that combines manufacturing and recycling industries within society. Specifically, the project will include the technology demonstration of the automated sophisticated dismantling process, the high-purity and re-resource processes for various materials extracted through advanced dismantling, and the prototyping and evaluation of parts made from these recycled materials. Additionally, the project will verify the sustainability of the whole process, evaluating how much carbon output it can reduce compared to current processes.
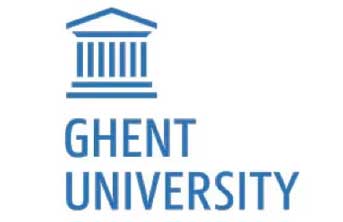
In other news, Mura Technology has signed a 5-year research partnership with the Laboratory for Chemical Technology (LCT) at Ghent University, an academic institution dedicated to minimising the environmental impact of chemical processes.
The research partnership will involve the construction of a continuous flow, pilot scale testing facility, which will be used for a range of research programmes to evaluate hard to recycle polymers, including complex composite materials. The results will help to drive future technology expansions and help Mura’s chemical partners understand the potential of products from circular feedstocks.
Mura Technology’s process, Hydro-PRT, is the next generation of advanced plastic recycling due to its use of supercritical water (water under elevated pressure and temperature), which distinguishes it from alternative recycling processes, such as pyrolysis.
The use of supercritical water ensures efficient and scalable conversion of plastic waste to hydrocarbons, enables the recycling of a wide range plastics, such as post-consumer packaging, and results in high yields of recycled hydrocarbons for use in the manufacture of virgin-quality, recycled plastics. Through this process, there is no limit to the number of times the same material can be recycled – meaning Hydro-PRT has the potential to significantly reduce the need for fossil resource in plastic production and permanently increase material circularity in the plastics industry.
By providing a route to recycle these hard to recycle materials, Mura has created a complementary process to operate alongside traditional mechanical recycling, as highlighted in the 2023 technical report by the European Commission’s Joint Research Centre.
This report also benchmarked Mura’s Hydro-PRT as the best in class, with a 50% lower carbon footprint, compared to two pyrolysis technologies, helping end customers to meet their Net Zero targets.
(IMA)Subscribe to Get the Latest Updates from IMA Please click here
©2024 Injection Moulding Asia. All rights reserved.