Green materials: Neste completes 2nd run of liquefied waste at Porvoo refinery; Birmingham University/Stopford allocated funding for chemical recycling tech
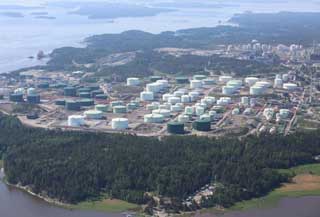
Finland’s Neste says it has successfully concluded its second series of industrial-scale processing runs with liquefied waste plastic at its refinery in Porvoo, Finland. The goal of the processing runs is to further increase the company’s understanding of how different types of waste plastics behave during chemical recycling in the refinery processes. The end product gained in the runs – Neste RE, a drop-in feedstock for petrochemicals – is turned into new plastics by Neste’s partners.
While Neste is establishing large-scale capacities to process liquefied waste plastic at its Porvoo site, the current processing runs utilise existing refinery equipment built for crude oil refining.
Since Neste’s first processing run in 2020, the company has concluded a total of six successful runs, processing close to 3,000 tonnes of liquefied waste plastic in total. After processing 800 tonnes in the first series completed in 2022, the company has been able to more than triple that amount to date. The processing runs are a part of Neste’s strategy to advance chemical recycling and contribute to a circular polymers economy.
“We are walking the talk on chemical recycling,” says Heikki Färkkilä, Vice President Chemical Recycling at Neste. “Our processing runs provide us not only with valuable knowledge on the technologies, but also serve as a proof of concept: chemical recycling can be done on an industrial scale. Our focus continues to be getting from individual processing runs to continuous operation.”
Neste processed so called “hard-to-recycle” waste plastic which would have ended up in incineration or landfill had it not been directed to chemical recycling. This highlights how chemical recycling complements existing mechanical recycling technologies.
The liquefied waste plastic for the runs has been sourced from multiple suppliers that are part of a supply network Neste has continuously expanded. Among others, the suppliers include US-based Alterra Energy, in which Neste holds a minority stake, as well as Finland-based Wastewise, with which Neste recently cooperated to chemically recycle cross-linked polyethylene (PEX) waste from pipe production into new PEX pipes.
Neste is looking to build capacities at its Porvoo site to process 400,000 tonnes/year of liquefied waste plastic in the course of project PULSE, which is funded by the EU Innovation Fund. From 2030 onwards, Neste wants to process more than 1 million tonnes/year of waste plastic.
This ambitious aim is an important part of the company’s strategic study to transition its Porvoo refinery into a renewable and circular solutions site and possibly end crude oil refining by the mid-2030s. Liquefied waste plastic would play an important role in replacing fossil crude oil in the company’s Porvoo refinery.
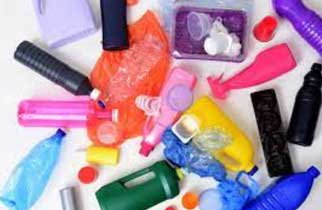
Meanwhile in other news, a research consortium comprising technologists from the University of Birmingham and engineering firm Stopford has been awarded a further £300,000 of funding from Innovate UK to develop a novel plastic recycling technology.
The technology is a chemical recycling process that utilises hot compressed water as green solvent to selectively depolymerise waste plastics into commodity compounds which can be processed to produce virgin materials – supplanting fossil fuel feedstocks and injecting much-needed circularity in plastic wastes management. Importantly, it is capable of recycling contaminated and degraded plastics, and requires reduced downstream processing.
To accomplish this, the process exploits the unique behaviour of water in its supercritical state (above a certain temperature and pressure) where it exhibits reduced polarity, high solvating power for complex polymers (like plastics). By virtue of combined intermediate heat and high pressure, it decomposes polymers at ‘selective spots’, thus producing target products at high proportions.
The new tranche of funding has been awarded by UK Research and Innovation’s Smart Sustainable Plastic Packaging Challenge to adapt its platform technology to PET-based plastic waste such as pots, salad trays, and tubs. It complements the team’s on-going work, also funded by Innovate UK, to establish a demonstrator facility at Birmingham’s Tyseley Energy Park for the recycling of polyolefin-based plastics, such as PP and PE, which are used in packaging.
Professor Bushra Al-Duri, Professor of Sustainable Process Engineering at the University’s School of Chemical Engineering and inventor of the platform technology said: “Supercritical water technology is exciting, intriguing, and challenging. We are dedicated to remain on the road of alleviating the upcoming challenges with science, engineering, and with working as one team of complementing skills.”
David Coleman, CEO at University of Birmingham Enterprise, said: “It’s great to see a technology invented in Birmingham coming full circle back to the city, which has fantastic facilities at the Tyseley Energy Park, and other spaces where companies can collaborate with the research base in a supportive environment.”
(IMA)Subscribe to Get the Latest Updates from IMA Please click here
©2023 Injection Moulding Asia. All rights reserved.