Thermoplastic Elastomers: TPEs drive brands’ sustainable goals
Without a doubt, the sustainability of plastics is critical to building a circular economy. Plastic material advancements ensure that plastics are imbued not only with appropriate mechanical properties, but also with attributes that align with the environmental goals of the entire value chain.
Thermoplastic elastomers (TPEs), in terms of processability and customisation, outperform thermoset rubber. Leading industry players are formulating new TPE grades and compounds that demonstrate versatility and durability while remaining non-toxic and recyclable, thus meeting the criteria for environmentally friendly materials.
According to research group Freedonia, TPE suppliers focusing on Asia will benefit from the region’s expanding markets, including motor vehicle markets in China, India, and Thailand, where TPE usage rates stutters behind those in developed countries. It forecasts a 3% annual growth to 7 million tonnes through 2024, owing to continued TPE penetration in both developing and developed economies, as well as the development of new TPE grades and compounds.
Sustainability an important factor
An example of sustainability being tackled in TPE grades is a new TPE formulation with recycled content, newly introduced by Avient, a US-headquartered manufacturer of specialised polymer materials. The reSound REC TPE formulation for use in certain food-contact applications has a Shore A hardness of 65 and contains 25% post-consumer recycled (PCR) PP content
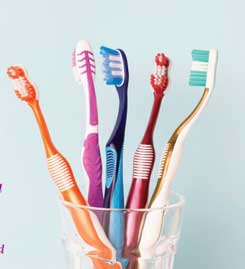
It has received a no objection letter (NOL) from the US FDA, which confirms that the recycled material included in this formulation can be used for manufacturing certain food-contact articles This grade is part of Avient’s reSound TPE portfolio, which also includes recycled-content and bio-based formulations.
This PCR content formulation, according to Avient, performs similarly to prime TPEs and can provide a more sustainable option in applications like toothbrush grips and other personal care items, as well as food-contact items like reusable crates. It’s naturally grey, colourable, and can be injection-moulded or overmoulded onto PP.
Environmentally-responsible materials
For Teknor Apex, being environmentally responsible is at the crux of sustainability goals of brands. Thus, the US-based compounder is putting forth its new Monprene TPEs that contain 25-35% recycled content, which meets consumer and regulatory demands for higher levels of recycled content in products. According to Teknor Apex, this significant added value helps brands achieve their sustainability goals.
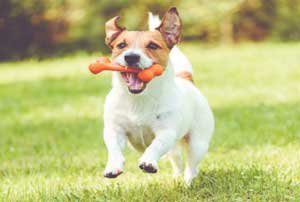
The Monprene RX CP-15100 series, formulated with PCR content allows brands to meet consumer and regulatory demands for recycled content within their products. These TPEs are available globally and manufactured around the world with locally sourced raw materials from waste diverted from households, or commercial, industrial and institutional facilities.
The Monprene RX CP-15100 series is available in standard grades from 55 to 80 Shore A, and can also be tailored for a customer’s specific requirements. Manufactured according to the standards of ISO-9001 and ISO 14001 in the US, Singapore and Germany, with strict formulation control and traceability, these grades are available in consistent light, natural colour, similar to their prime offsets.
They are designed for injection moulding applications, including overmoulding onto PP. The grades are said to perform and process like prime TPE and are ideal for personal care products, lawn/garden tools, writing instruments, appliances, sporting goods and dunnage. Teknor Apex says Monprene RX not only reduces plastic waste but also ensures that products are fully recyclable at the end of their useful lives
Likewise focused on delivering TPE solutions for an eco-conscious market, United Soft Plastics (USP), a US manufacturer and custom compounder of TPEs has developed a series of sustainable solutions, produced from renewable, post-consumer, post-industrial, and biobased sources.
Its first commercially available grades, based on styrene-ethylene-butylene- styrene (SEBS), are made of up to 100% PCR and post-industrial materials. The grades have the typical soft touch, anti-slip properties, adhesion, and haptics. The injection moulding grades are available in 45-65 Shore A hardness and are suitable for a variety of consumer applications, including personal care.
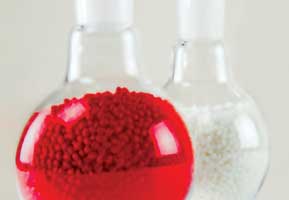
Three other series of sustainable TPE solutions are currently being commercialised. These low-cost SEBS grades contain up to 70% renewable products such as wood flour, rice hull, and/or hemp. These have a limited performance threshold, which excludes use in highly engineered TPEs.
Also in commercial development phase are biopolymers, which utilise non- fossil-based materials with up to 100% content. These biobased TPEs deliver almost similar performance as standard materials for injection moulding applications (although available quantities are limited), and hold considerable potential of market impact and carbon emission reduction, USP said.
Bio-hybrid TPEs, which can combine renewable, post-consumer, post-industrial, and biobased content up to 100%, are also included in USP’s sustainable TPE portfolio.
(IMA)Subscribe to Get the Latest Updates from IMA Please click here
©2022 Injection Moulding Asia. All rights reserved.