Industry 5.0: Human touch in robotic-enabled industries
Through collaboration with robots, human ingenuity unlocks the key to increasing manufacturing efficiency and sustainability, adds Angelica Buan in this report.
Robots uprising: threat to human jobs?
The fourth industrial revolution (Industry 4.0) has been a game changer in reshaping smart industries, which aim to improve productivity by enabling collaboration and data sharing among vendors, producers, suppliers, and other entities in the supply chain, with the help of big data, artificial intelligence (AI), and the Internet of Things (IoT).
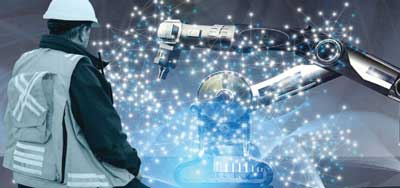
Robotics is an integral automation technology in Industry 4.0. Robots can perform high-volume, repetitive tasks with greater accuracy and at a relatively low cost and are now used throughout the advanced process chain, from part installation to packing and labelling, to ensure consistent and timely production, shorter cycle times, and higher throughput.
The dominance of robots in automation systems has ignited concern, particularly about impact on the workforce. In the face of a labour shortage, robots are widely perceived to displace workers or low to mid-skilled jobs, and are discreetly viewed as competitors, particularly because they are less likely to make errors than humans. An AI takeover or a robot uprising, according to conspiracy theorists, is plausible in an Industry 4.0 scenario.
In his 1930s essay, Economic Possibilities for our Grandchildren, English economist John Maynard Keynes speculated that growing technological innovations, such as automating industrial processes with “less human effort”, would lead to “technological unemployment” - owing to the “discovery of means of economising the use of labour.” The current ambivalence about robots’ hegemony in the manufacturing space can be summed up in this statement.
Labour-intensive cobots
Nonetheless, several companies struggling from labour gaps are adopting robots to augment manpower for demanding tasks and avoid operational downtimes. Especially during the Covid-19 pandemic, companies that had to deal with challenges of rising delivery expectations, and expanding order volumes, turned to collaborative robotics (cobots) manufacturers like Universal Robots, to provide them with required automated solutions.
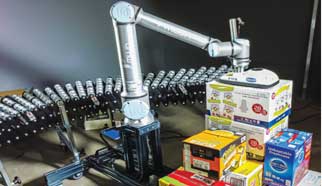
Last year, Denmark-headquartered Universal Robot demonstrated its automated solutions for hard-to-staff tasks, such as box erecting and palletising. The UR10e has a 25% increase in payload at 12.5kg, which translates to moving more per pick, usage of heavier tools, and processing heavier parts, supported by the 1,300 mm reach and small footprint.
According to the cobot manufacturer, the enhanced UR10e’s greater payload also takes more weight off from the hands and shoulders of humans, leading to improved ergonomics and working conditions.
Humans, driving force in innovations
If Industry 4.0 is defined by digitalisation, the fifth industrial revolution or Industry 5.0 is defined by personalisation. This new production model reflects the need for industries to meet the rapidly changing needs of markets. Industry 5.0 also emphasises the importance of human labour in the expansion of industrial manufacturing
While robots remain an essential component of Industry 5.0, they are not presumed to be superior to their operators. Robots are used for menial, redundant jobs and even tasks in hazardous environments where humans are not present.
The benefit of industrial robots in this context is demonstrated in Stäubli Robotics’s robots to make demanding processes more efficient.
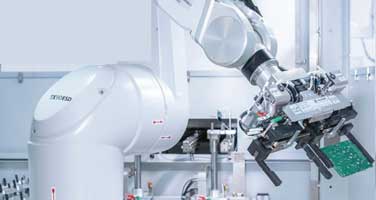
For example are Stäubli’s Electro Static Discharge (ESD)-variants of its Scara and six-axis robots for use in in all possible areas of the electronics and battery sectors. Stäubli’s larger TX2-140/160 six-axis robots, as well as the TX2-40, TX2-60 and TX2-90 models, which are UL certified and comply with safety level SIL3/PLe, have been developed for assembly, testing and packaging processes of sensitive electronic components – from control units and various assemblies to battery packs.
The four and six-axis robots are designed to prevent ESD in order to safely handle electronic components. They can operate in EPA (ESD protected area) for various applications such as PCB assembly, any kind of part inspection or testing and packaging of electronic consumer goods.
Robotic solutions, such as those provided by Stäubli, protect employees while also increasing output productivity. Human workers can be reassigned to appropriate roles in engineering, programming, administration, and technical support as a result of the implementation of robots.
In short, Industry 5.0 exemplifies a positive, cooperative relationship between automation systems and human intelligence, as well as the fact that humans are the driving force behind technological advancements.
(IMA)Subscribe to Get the Latest Updates from IMA Please click here
©2022 Injection Moulding Asia. All rights reserved.