Automotive: EV adoption and sustainability reinforce automotive plastics industry trends
Robust automobile demand in APAC and Middle East regions and an increasing acceptance of electric mobility will influence automotive plastics demand, says Global Market Insights in this article.
The global focus on carbon footprint reduction has pegged the transportation sector as a key target, invariably shifting the crosshairs on automotive plastics industry. The symbolic Paris Agreement on climate change has set out bold targets over the coming decades, with the overall goal of carbon neutrality by 2050. The IEA reports that around 18% of direct CO2 emissions worldwide are from road vehicles and gradually, investments toward making considerable advancements and adjustments in vehicle production have taken a front seat.
Apparently, emissions from transportation grew by less than 0.5% during 2019, which was a promising statistic considering the 1.9% annual increase since 2000. The major reasons behind this are improved efficiency, electrification as well as a growing adoption of biofuels. From these factors, better efficiency of ICE automobiles is achieved through several ways, including the change in materials used for manufacturing certain components.
Automotive plastics
Automotive plastics have captured a notable share of the total vehicle configuration, replacing heavier metal options like steel in some critical components. The applications of polymers in automobile include many electrical components, power train and even the chassis, apart from numerous interior and exterior aesthetic parts. Under the hood parts like pipes, connectors and cables, manifolds, cam covers, fluid tanks, among others are being produced using plastics. It is, therefore, become necessary to study the latest trends in automotive plastics market and understand the mutual impacts it has on the developments in the transportation domain.
In regions like Asia Pacific (APAC), the Middle East and Africa (MEA), where new vehicle production and sales is expected to grow at a substantial rate, efforts for enhancing fuel efficiency and promote vehicle electrification will undoubtedly foster the consumption of plastic components. These regions are also home to a large number of chemical companies and polymer manufacturers, which seconds the above argument.
ABS emerges as a preferred polymer
Considering the importance of vehicle safety and durability over a long term, the selection of base materials is critical. Acrylonitrile butadiene styrene (ABS) is a thermoplastic exhibiting high impact strength and toughness, making it a strong candidate for numerous automotive applications. Some of these uses include dashboard parts, door handles and liners, seat belt parts, instrument panel components, among others.
Substituting polymers for metals in these applications can help lower the overall vehicle weight noticeably. ABS has robust physical properties like good insulation, impact resistance, weldability, abrasion resistance and high rigidity. It is consequently one of the clearer alternatives for metallic components. A crucial factor expanding ABS consumption in APAC and MEA is the presence of notable manufacturers of the substance, such as Sabic, Mitsui Chemicals, CHIMEI, Asahi Kasei Corporation, China Petroleum & Chemical Corporation, Kumho Petrochemical and LG Chem.
The most commonly known benefit of plastic materials is reduced fuel consumption and emissions due to lighter vehicles. However, they can also enhance the safety parameters to a great extent. For instance, car bumpers manufactured using polymers like ABS, PP, PU and others, combined with glass fibres can absorb up to five times more energy on impact, while weighing up to 50% less.
Reportedly, a new car with around 1,500 kg weight can comprise of up to 20% of plastic materials, with the percentage expected to go up as more innovations are made in the transportation sector. The scope for ABS demand is certainly strong over the next few years, with trends like EVs and hydrogen-cell powered vehicles taking shape. According to Global Market Insights Inc. (GMI), the share of ABS in automotive plastics industry will record a promising 10.5% CAGR up to 2027
Electrification of vehicles to augment automotive plastics outlook
Referring again to the 2050 carbon neutrality agreements, one of the milestones in the strategy is ensuring that nearly 60% of all car sales worldwide are electric by 2030. That target does not seem farfetched anymore, as almost 6.5 million plug-in and fully electric vehicles we sold during 2021, which was a 109% jump over the previous year. With numerous EV and autonomous transportation start-ups taking birth globally, these numbers will only go up.
Even major automakers from countries like China, India, South Korea and Japan are speeding up their electrification efforts. China’s BYD has confirmed the launch of three new EVs this year alone, whereas other brands in the region like Geely and MG also making strong moves. Tesla already has a major presence in the country. In India, Tata Motors has found tremendous success for its new EV models, while brands such as Hyundai and MG have also registered increasing sales here.
Since a common ICE private or commercial vehicle already boasts a significant share of plastic components, the use of these materials in EVs will definitely go higher with the elimination of metal-intensive components like the engine, gears and the traditional axels. However, EVs usually become heavier than ICE vehicles, due to the addition of large battery packs and other electrical components. As such, the onus of reducing the weight of electric cars, to enhance the driving range per charge, falls highly on plastic materials.
For EVs, lightweighting by around 10% can enhance the driving range by close to 13.7%. Demand for battery packs with lower weight will be a prime factor impacting plastics consumption, since they are one of the heaviest components in an EV architecture.
On the other hand, efficient cost cutting measure can help enhance the manufacturing process by using materials which meet the recommended physical characteristics but are not high-cost engineered polymers. For instance, electric cars do not require as much under-the-hood temperature resistance compared to ICE vehicles, bringing into focus plastics like PA in place of PP or PU. Nylon/PA is being widely utilised for battery brackets and other enclosures for EVs.
As evident, the emerging trend of EVs and autonomous vehicles will present a vast challenge in terms of lightweighting strategies, albeit offering considerable opportunities for automobile plastics manufacturers from applications like electric component housings, battery racks, energy storage systems, charging stations, as well as innovative solutions like swappable battery stations.
Evaluating automotive plastics industry scope across APAC and MEA
According to OICA, more than 3.02 million vehicles were manufactured during the first three quarters of 2021 across China, India, Japan, Malaysia and South Korea. The figures represent a considerable recovery from the Covid-19 pandemic impact. EVs adoption has been observed as a widespread trend across the APAC region, influencing the automobile materials segment to a large extent.
The Middle East region is not behind in pursuing electric vehicle adoption, in line with the climate goals of regional governments. Saudi Arabia has set a target of ensuring EVs make up nearly 30% of regional car sales by 2030. Further, an Audi Abu Dhabi survey in 2021 revealed that more than 29% residents in the UAE are ready to purchase an EV.
GMI estimates that APAC automotive plastics market size could witness more than 9.5% CAGR through 2027, while the market in MEA region will expand at a robust 12% CAGR.
The strong support for future mobility across the APAC and MEA has encouraged polymer companies to invest in developing suitable products, expand capacities, undertake major deals and partnerships, among other strategies to strengthen their position in automotive plastics industry. Some of these companies include BASF, Sabic, Solvay, Dupont, LG Chem, Arkema SA, Evonik Industries and Teijin Limited, among others.
Sabic, one of the largest chemical names worldwide, has recently introduced a PC alternative for replacing glass in automotive applications. The company conducted a study on rear-quarter windows and found that the new PC material provides better lightweighting, cost benefits and design flexibility as compared to glass.
In another example to tackle weight reduction goals of customers, Sabic also partnered with China’s Dongfeng Motors for the development of a long glass fibre PP for a glass composite. The material can be used in making a strong, light-weight toolbox to be mounted on trucks, being 30% lighter as compared to the same design made using steel.
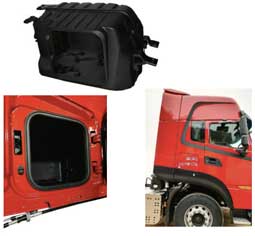
In terms of upcoming trends, the increased focus toward plastics recycling can also impact automotive plastics market forecast over the next few years. LG Chem has already announced its entry into the chemical recycling sector with the construction of a plastics recycling facility in South Korea, to enable plastic waste to be upgraded into new plastics. Sabic, too, has made progress in the foray and has introduced automotive grade PC and PP resins containing up to 29% recycled content.
Although the Covid-19 outbreak in 2020 has dented the manufacturing sector to a large extent, the resumption of production units and supply chains has been at a commendable rate. The economic importance and robustness of the transportation sector will sustain automotive plastics market growth, while emerging trends in innovations and sustainability alter the overall industry dynamics over the coming years.
(IMA)Subscribe to Get the Latest Updates from IMA Please click here
©2022 Injection Moulding Asia. All rights reserved.