Cost-effective IML system for 5 gallon pails
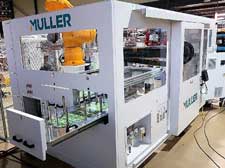
US-based Muller Technology, a specialist in tool making and automation technology for thinwall plastic packaging, has launched an in-mould labelling (IML) automation system for the production of 5-gal pails that is said to reduce cost, improve productivity, and enhance graphics and product appearance. Muller’s new IML system is claimed to offer major improvements over standard pressure-sensitive and printed systems that are time-consuming and require double handling of parts.
Unlike Europe, where IML has gained strong penetration in a range of packaging applications, Muller notes that the technology has been slower to develop in North America. However, label suppliers are predicting 40% growth in North America this year for industrial pail IML with brand owners and moulders driving the demand, according to Taras Konowal, Muller’s North America Director of Sales and Marketing.
“Our IML technology enables pail manufacturers to add to their product offering without any infrastructure changes, enabling them to maintain a small footprint and limiting costly scrap,” said Konowal.
Muller responded to customer needs with a one-piece IML system which is less than 8-ft wide compared to competitive IML systems that are 12-14 ft wide. It fits conveniently into non-IML production lines, requires no adjustment in floor layout, and fits any injection moulding machine height. The IML system places the wrap-around polypropylene (PP) label into the mould, removes the pail after moulding, and transports it to a visual inspection station. The pail is then directed to stacking and handle assembly. Systems can be easily converted from one cavity to two cavities to enable the production of 1 to 5-gal pails.
Manufacturers often face the costly scrapping of a finished pail due to label misalignment. Muller adds that a key feature of its IML system is digital label placement positioning that provides significant precision and detailed label placement versus standard, manually adjusted magazines. The system also has quick change-out capability from pail size to pail size and label to label. Rotating dummy mandrels allow label seams in different locations.
Muller says it has already sold IML systems to leading manufacturers in the US and South Africa. The company builds these systems in the US at its Fort Collins facility and in Switzerland at its Conthey plant.
Muller Technology Colorado (formerly CBW Automation), based in Fort Collins, Colo., focuses on injection moulding and thermoforming applications in the packaging and medical sectors.
Swiss-based Muller Technology Conthey (formerly H. MÜLLER-Fabrique de Moules SA) was founded in 1959 and is a pioneer in the field of packaging design, mould, and automation solutions for injection moulded thinwall packaging with leading-edge expertise in in-mold-labelling (IML).
(IMA)Subscribe to Get the Latest Updates from IMA Please click here
©2021 Injection Moulding Asia. All rights reserved.